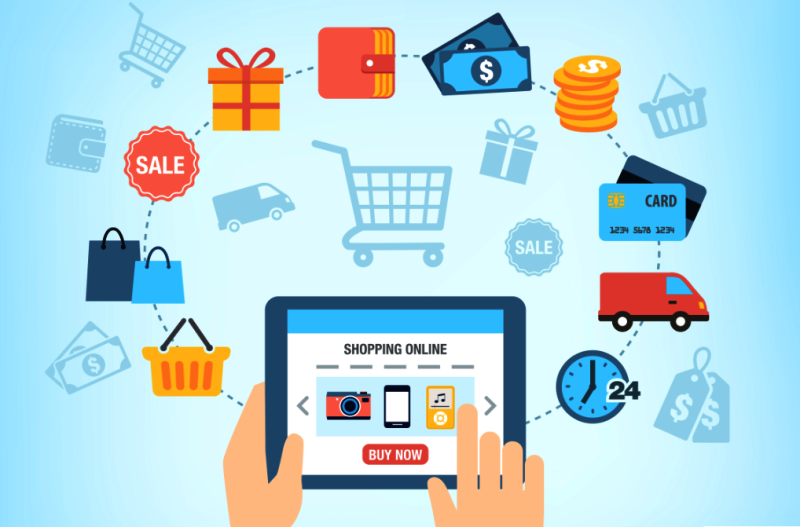
The e-commerce, electronic commerce, is gaining the game to physical stores and already accounted for about 20% of the volume of card sales in 2018, while in 2015 this fee was 11% of transactions.
Concerning on the situation of consumption in the second semester affirms that the turnover of electronic commerce was close to 35,000 million in mid-2018, which multiplied by 7.5 the figure recorded in 2008, and the penetration rate exceeded for the first time the 50% of the population between 16 and 74 years old to be 53%, which is 18.5 million people and 35 percentage points more than in 2008. These data contrast with the evolution of the turnover of the trade traditional retail, which fell more than 4% in the same period in the last decade, and the meager growth of the population between 16 and 74 years (0.3%).
E-commerce is increasingly used by the users of the network, due to the great ease that this delivers, it is not necessary to go off to visit the physical store incurring in additional costs in terms of time and money, which can be saved through a single click on the website of the desired store.
Capture, maintain and retain customers is a task of great importance, the process of delivery of the products is directly related to the above. Because this process must be efficient and performed in the time specified by the seller, otherwise, if the customer has a bad experience with the delivery process either by a delivery in hours not accrued, couriers who do not locate the customer or products that do not comply with the advertised characteristics, this customer may generate the loss, which he will not buy again in the online shop.
There are solutions to avoid the situations mentioned above as the Click and Collect service, this is a system that benefits both, the companies that make online sales, as well as the customer who makes purchases in these. Since it provides flexibility to the consumer, allowing the collection of the package in the place that suits best and in the schedule that best suits their needs. Generally, these points are located throughout the cities and even in the same physical stores in order to have the closeness to consumers.
Another alternative to solve these problems is the service of lockers located equally in different points of the cities, which have been enabled through agreements with establishments in which the lockers can be placed. The big companies in Spain such as Amazon and Correos have this service called “Amazon Locker” and “CityPaq”.
As a conclusion, it can be said that currently, it must evolve on a par with the technology and the needs of consumers, in order not to become obsolete and to be left out of the market.